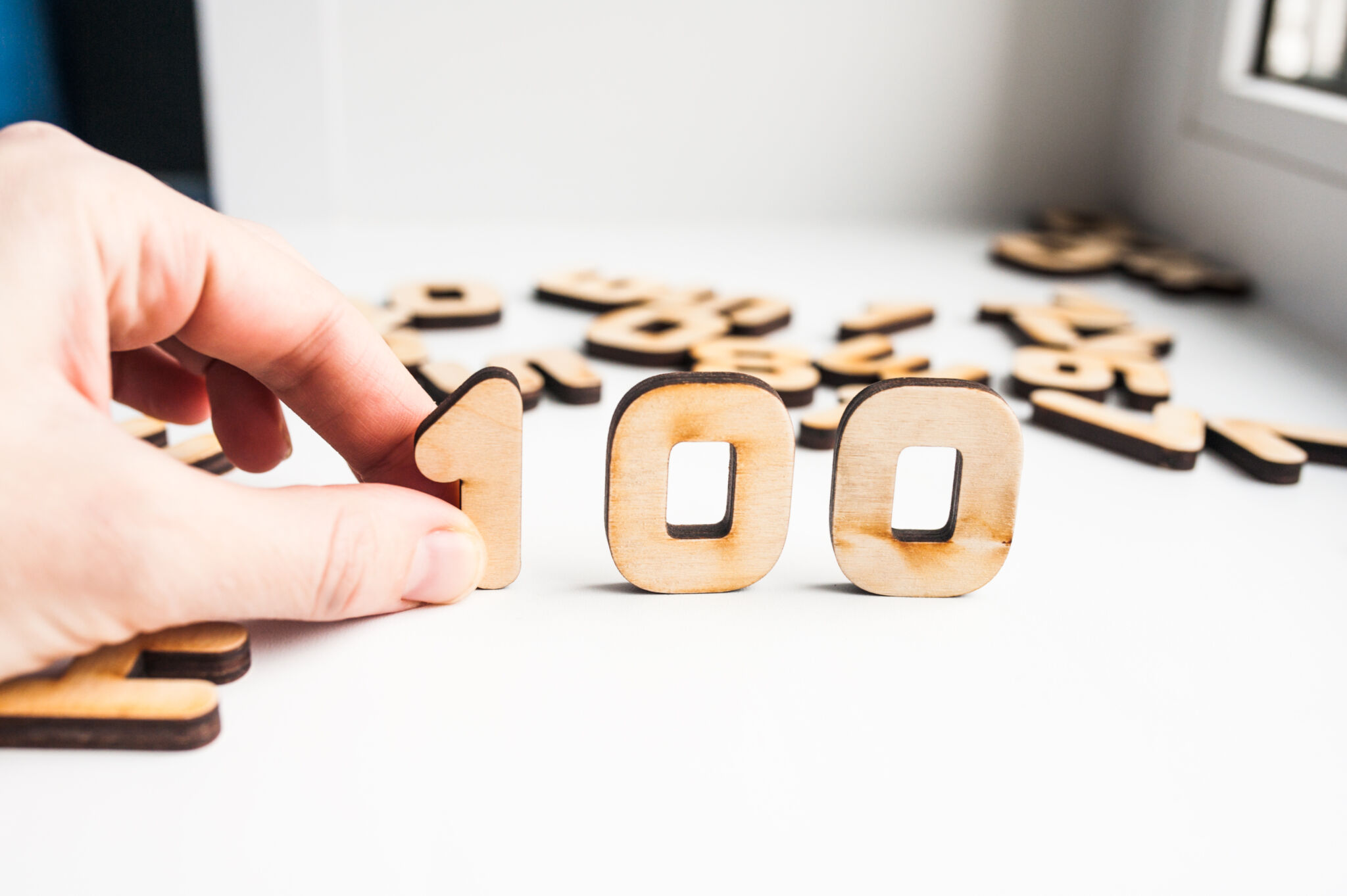
100ème newsletter ! Déjà ! Tout d’abord, je souhaiterais vous remercier de votre fidélité à nos éditos et nos évènements. Nous ne serons jamais assez pour essayer d’infléchir la trajectoire de notre industrie – ou ce qu’il en reste après sa démolition systématique par les grands patrons industriels qui étaient censés la protéger. Que dire d’autre après tant d’éditos sinon : apprenez le lean, pratiquez le lean, enseignez le lean.
Le lean est un ensemble de principes et méthodes de management dont le but est de coller toujours plus au marché tout en réduisant sa base de coûts globale. Toyota l’a développé depuis les années cinquante, et nous montre encore chaque année que cette méthode lui permet d’essuyer les mêmes crises globales que les autres, tout en continuant de servir ses clients avec de meilleurs produits, à grande échelle et avec la rentabilité d’une boutique de luxe.
Dès qu’un patron fait l’effort d’apprendre leur système, ses résultats sont rapides, visibles et durables, même au sein d’une grande entreprise traditionnelle. Mais dès qu’il ou elle part à la retraite, les résultats reviennent à ce qu'ils étaient avant son arrivée – les mêmes causes ont les mêmes effets. La seule difficulté est de faire l’effort d’apprendre un système de management qui n’est ni enseigné par les grandes écoles, ni pratiqué par la plupart des managers, bien qu’il soit extensivement publié et décrit depuis longtemps : les livres sont là, Toyota continue de développer son système, d’en montrer les résultats et de l’enseigner à qui s’y intéresse. Bref, il faut faire l'effort d’ouvrir un livre, puis un autre, puis un autre – trop demander à un grand chef payé des milles et des cents pour faire son job ?
Pourquoi faire l’effort ? Dans les années soixante-dix, Freddy Ballé, alors patron de la planification produit à la régie Renault, découvre accidentellement le « lean » (le terme ne devait apparaître que 15 ans plus tard) dans les usines Toyota au Japon. Il y voit tout de suite une entreprise déjà très performante dont les circonstances sont similaires à celle de Renault en France, un petit marché qui n’a :
● Pas la dimension américaine
● Pas les moyens américains
● Pas la facilité américaine de vivre avec des relations industrielles conflictuelles sans que cela ne les arrête (ou du moins à l’époque, car comme on sait l’histoire finira par les rattraper)
En somme, une entreprise nationale qui a des rêves d’expansion internationale mais qui n’en a pas les moyens, ni en produit, ni en production, ni en distribution (hormis l’Afrique, à l’époque chasse gardée des constructeurs français que Toyota commence à attaquer – et qui amène mon père à visiter leurs usines).
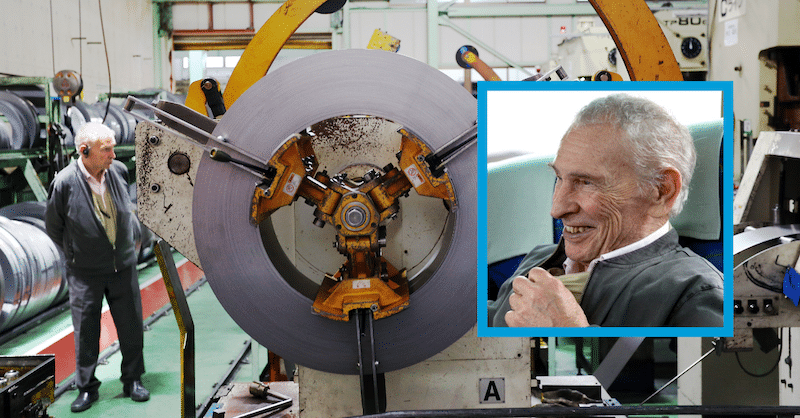
Tout au long de sa carrière Freddy Ballé n’a eu de cesse de comparer, face aux mêmes problèmes du fait d’une position mondiale similaire dans le monde après-guerre, les réactions de Toyota et des constructeurs français :
- Toyota a des problèmes de qualité ? Ils choisissent de les aborder de front en allant chercher le prix Deming, là où nous expliquons que notre qualité est déjà meilleure que celle de nos concurrents (donc pas la peine de faire un effort supplémentaire).
- Toyota subit une grève terrible ? Ils décident que les superviseurs locaux doivent devenir des partenaires des syndicats pour résoudre les conflits à leur source, là où nous pensons que les affaires syndicales sont si importantes que seul le grand patron peut les régler.
- Toyota subit les augmentations de coûts des chocs pétroliers ? Ils en concluent qu’il faut enseigner son système à son tissu de fournisseurs et créer des partenariats, alors que nous renforçons la fonction Achats pour mieux les saigner, sans réaliser que nous nous privons ainsi de l’innovation technique des fournisseurs qui détermine pourtant notre futur.
- Toyota se plante avec une voiture ridicule sur le marché américain ? Ils décident d’y revenir avec une voiture compétitive, y introduisant progressivement la Corona et la Celica qui cartonnent – les constructeurs français essayent de faire des alliances stratégiques qui échouent, puis se retirent.
- Toyota ne parvient pas à pénétrer le marché haut de gamme face aux constructeurs allemands ? Ils créent un nouveau moteur puissant pour les affronter avec Lexus, en décrochant un succès sans pareil, alors que les constructeurs français continuent d’expliquer que le luxe est une question d’élégance du design et de la boîte à gants, pas de motorisation.
- Toyota décide de s’internationaliser ? Ils misent sur l’implantation d’usines dans chaque marché ciblé, alors les constructeurs français cherchent des stratégies d’acquisitions financières – avec tout le succès qu’on leur connaît.
Bref, la liste est longue et si mon père n’était pas décédé, il en trouverait sans doute à rajouter. Ce qui le rendait particulièrement fou furieux est notre indifférence à l’échec – nos grands managers valorisent plus le fait d’avoir raison sur le moment et de passer en force que de gagner sur le fond. Il a passé sa carrière à démontrer que les méthodes de Toyota – le lean – étaient tout aussi efficaces en France qu’ailleurs, à avoir des résultats spectaculaires, et être très largement ignoré par ses pairs. Le seul commentaire que m’ait fait le seul de ses anciens collègues présent à son enterrement est « il s’est quand même fait beaucoup d’ennemis. » (certes, ai-je pensé, il avait aussi souvent raison).
Mon père avait saisi, dès ses premiers séjours au Japon, que Toyota, n’ayant pas les moyens de faire de la production de masse sans s’allier à des fournisseurs américains, avait inventé un système de production artisanale à grande échelle :
- Chaque client doit trouver la voiture qui lui convient et être satisfait de sa qualité
- Chaque produit est assemblé un par un sur des cellules multi process (le travail est essentiellement mené par des machines, mais l’opérateur reste menant et garant de la qualité)
- Chaque changement provenant de l’ingénierie doit être perfectionné par une collaboration sur le terrain entre l’ingénieur et les opérateurs (le kaizen que nous avons tellement de mal à reconnaître en visitant les usines de Toyota au Japon)
- Chaque fournisseur est un partenaire technologique (et pas une opportunité de moins s’en occuper en serrant les prix)
- Chaque coût issu de mauvaises décisions doit être exploré et éliminé
Toyota l’explique depuis longtemps : l’enjeu est de préserver le soin de l’artisanat malgré le volume.
Cet engagement a conduit Toyota à développer des techniques de management très spécifiques :
- Une gamme large, très précise, correspondant à des segments sur chaque marché avec de nouveaux véhicules proposés à un rythme régulier, et un chief engineer (pensez artisan / artiste) qui « signe » chaque nouveau modèle.
- Un arrêt au défaut permettant de développer la responsabilité qualité des opérateurs (apprendre à reconnaître soi-même les défauts) et le soutien de la chaîne hiérarchique pour résoudre tous les problèmes au fil de l’eau (comme un maître artisan qui corrige et enseigne à son apprenti)
- Un système de juste-à-temps dans lequel les pièces et matières ne sont « tirées » par un kanban que lorsqu’elles sont nécessaires pour produire, en petites quantités régulières et non en grands stocks soi-disant économiques.
- Du kaizen (de l’amélioration par petit pas) pour faire en sorte que chaque changement d’ingénierie soit peaufiné par les équipes de production pour atteindre le niveau de fluidité de production d’avant le changement.
- La formation intensive de chaque personne de l’entreprise et un système de développement des carrières en fonction des souhaits, compétences et capacités de chacun.
- Des techniques de flux tiré et d’auto-qualité étendues à l’ensemble du tissu des fournisseurs – jusqu’à s’attendre à ce que les fournisseurs de rang un et parfois deux proposent des innovations sur étagère à intégrer aux nouveaux produits en développement (ce qui nécessite de leur laisser assez de marge pour vivre, et, avec la Chine en face, conduit souvent à faire intensément du kaizen chez eux pour baisser les coûts).
Bref, ce n’est pas mystérieux et ça s’apprend, mais l’apprendre requiert une révélation préalable : adopter des techniques de production de masse sans avoir les volumes nécessaires face à des concurrents américains ou chinois qui, eux, ont tout le volume qu’il leur faut – n’a jamais et ne pourra jamais gagner.
Le rêve de Tesla – la Tesla que vous voulez tant que c’est un modèle Y noir (ou blanc) – n’est autre que le rêve de Ford au goût du jour : une gamme réduite, des produits très bien conçus fabriqués dans des usines entièrement automatisées. Ce rêve séduit toutes les petites grenouilles qui veulent se faire aussi grosses que les bœufs, mais il ne peut aboutir car, tout simplement, la taille des marchés n’est pas là. D’ailleurs ce n’est pas par hasard si nos entreprises qui s’en sortent sur les marchés internationaux sont dans le luxe et très attachées à leur… artisanat.
Dans ce contexte économique tendu, comment réagir ? Regardez vos clients, regardez vos équipes : les premiers veulent que l’on s’intéresse à eux, les seconds que l’on valorise leur travail et leur expertise. L’envie est là, la méthode est là, il n’y a plus qu’à changer le film de nos dirigeants et nos managers pour adopter enfin le modèle du 21e siècle : la production artisanale à grande échelle.
Apprenez le lean, pratiquez le lean, enseignez le lean !
Michael Ballé
Télécharge l'édito en PDF.
Cet article L’ère de l’artisanat à grande échelle est apparu en premier sur Institut Lean France.
A lire aussi
-
Ne pas confondre Lean et gestion des stocks
Publié le 06/12/2018
Cher Gemba Coach Notre nouveau patron est un adepte du Lean et nous a fait réduire...
-
Deux questions, deux trajectoires
Publié le 03/09/2024
« Vous avez fait ce que vous aviez à faire ? Montrez-moi vos indicateurs...
-
Quand faut-il utiliser le A3 ?
Publié le 29/11/2017
Cher Gemba Coach, J’aimerais vraiment avoir votre avis sur les points suivants:...
-
Hoshin Kanri : que faire en cas d’échec ?
Publié le 24/09/2017
Comment poursuivre notre Hoshin Kanri quand les choses ne se passent pas comme...
-
“Monozukuri” : Pourquoi ne pas parler français ?
Publié le 27/07/2017
Cher Gemba Coach, Pourquoi vous obstinez-vous à utiliser des termes japonais...
-
L’intelligence collective est une compétence individuelle
Publié le 02/04/2024
Qu’est-ce qu’une intelligence collective ? Le sujet revient souvent, mais...
-
Des opérations Commando… pour surtout ne rien apprendre !
Publié le 04/02/2021
Il y a quelques semaines, j’ai eu un échange avec un directeur régional au sujet...
-
Publié le 04/11/2024
En matière de combat contre le changement climatique, nous ne pouvons espérer...
-
Comment avoir des standards quand il n’y a pas deux cas identiques dans des activités de services ?
Publié le 10/10/2019
Cher Gemba Coach, Je travaille dans le secteur des services, et j’ai des...
-
Devenir meilleur dans son métier grâce au standard
Publié le 08/04/2025
Lundi, 15h52. Nouvel e-mail dans ma boîte de réception : « Bonjour Camille,...